Build A Info About How Many Wires Can You Put In A Terminal

Understanding Terminal Wire Capacity
1. The Big Question
So, you're staring at a terminal block, a handful of wires, and that nagging question: "Just how many of these little guys can I cram in here?" It's a legitimate concern! Overstuffing a terminal isn't just bad practice; it can lead to loose connections, overheating, and potentially even electrical fires. Not exactly ideal, right?
The truth is, there's no one-size-fits-all answer. The number of wires a terminal can safely accommodate depends on a bunch of factors. We're talking terminal size, wire gauge, wire type, and even the specific terminal block manufacturer's recommendations. Think of it like trying to fit suitcases into your car trunk — a couple of smaller ones might fit nicely, but trying to force in too many big ones will just lead to frustration (and maybe a broken zipper!).
Before you start shoving wires in, take a close look at the terminal block itself. Often, the manufacturer will have stamped information directly onto the block, indicating the wire size range it's designed for. This is your golden rule! Ignoring this is like disregarding the speed limit — you might get away with it for a while, but eventually, you're going to run into trouble. Check the product manual or the manufacturer's website for the exact specification of the wire it supports. Do not rely on guesswork!
Also, consider the type of wires you are using. Solid core wires are typically easier to secure, and they often provide a more reliable connection than stranded wires, especially if the stranded wires aren't properly terminated with ferrules. Each type of wire has specific use case, and they should be used accordingly for reliable performance and safety.

How Many Wires Can I Put In This Box? To Calculate Box Fill The
Key Factors Affecting Wire Capacity
2. Decoding the Wire and Terminal Specs
Let's dive a little deeper into those factors that determine how many wires you can safely put in a terminal. Wire gauge is a big one. This refers to the thickness of the wire. Thicker wires (lower gauge numbers) can carry more current, but they also take up more space in the terminal. Trying to jam a thick wire into a terminal designed for thinner wires is a recipe for a loose connection and potential problems. It would be like trying to screw a bolt into a nut that's too small - it just won't work.
Terminal size is another obvious consideration. A larger terminal block will generally accommodate more wires, or larger gauge wires, than a smaller one. But even within the same size range, there can be variations. Some terminals are designed with multiple connection points, allowing you to connect several wires to a single terminal position. These are super handy for distributing power or signals to multiple devices. However, again, don't exceed the manufacturer's specified capacity. Doing so will defeat the purpose of the design.
Then there's the issue of wire type. As mentioned earlier, solid wires and stranded wires behave differently. Stranded wires, especially when not properly terminated with ferrules, can splay out and make it difficult to achieve a secure connection. This can also increase the risk of short circuits if stray strands come into contact with other conductive surfaces. Ferrules are crimped onto the end of stranded wires to create a solid, secure termination that fits neatly into the terminal block.
And let's not forget about the terminal block's design. Some terminal blocks have screw-down terminals, while others use spring clamps or push-in connectors. Each type has its own advantages and limitations regarding wire capacity and ease of use. Spring clamps, for instance, can be quicker to use, but they might not be suitable for very thick or very thin wires. Refer to the manufacturer's instructions on the proper way to insert the wires into each type of terminal to ensure secure and reliable connections.
Best Practices for Safe Wiring
3. Ensuring Reliable Connections
Okay, so you know the factors involved. Now, let's talk about some best practices for making sure your wiring is safe and reliable. First and foremost, always consult the manufacturer's specifications for both the terminal block and the wires you're using. This is your bible! Don't rely on guesswork or assumptions.
Secondly, use the correct tools for the job. A proper wire stripper will remove the insulation without damaging the conductor. A good crimping tool will ensure that ferrules are securely attached to stranded wires. Using the wrong tools can lead to damaged wires, loose connections, and potential safety hazards. It's like trying to cut a steak with a butter knife — you might eventually get the job done, but it won't be pretty, and you'll probably end up with a dull knife.
Thirdly, strip the wires to the correct length. Too much exposed conductor can create a risk of short circuits, while not enough exposed conductor can lead to a weak connection. The terminal block manufacturer usually indicates the optimal strip length in the product documentation. Follow their guidelines carefully to avoid any problems.
Fourth, after inserting the wire into the terminal, give it a gentle tug to make sure it's securely held. If it pulls out easily, something is wrong. Either the wire isn't properly seated, the terminal screw isn't tightened enough, or the wire is too small for the terminal. Take the time to correct the issue before moving on. A loose connection is a ticking time bomb waiting to cause problems down the line. It's far better to fix it now than to deal with the consequences later.
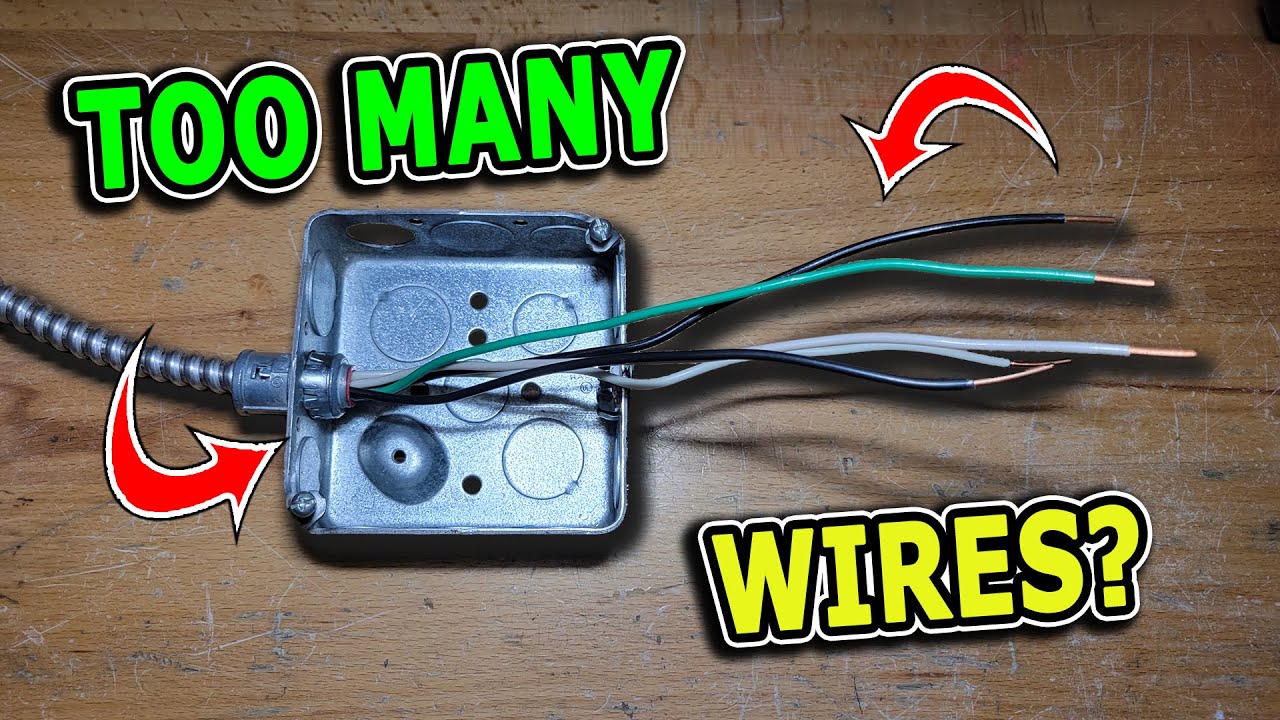
Common Mistakes to Avoid
4. Steering Clear of Wiring Woes
Even with the best intentions, it's easy to make mistakes when wiring terminals. One common error is over-tightening the terminal screws. This can damage the wire, the terminal block, or both. It's especially problematic with smaller gauge wires, which are more easily crushed. Tighten the screw until it's snug, but don't crank it down with all your might. Think of it like tightening the lug nuts on your car wheels — you want them tight enough to be secure, but not so tight that you strip the threads.
Another mistake is using damaged or corroded wires. These wires are more likely to break or corrode further, leading to a unreliable connection. Always inspect the wires carefully before using them, and discard any that show signs of damage. Using old or corroded wires is like building a house on a shaky foundation — it might seem okay at first, but eventually, it will crumble.
A further error is mixing different wire gauges in the same terminal. While it might seem convenient, this can create an uneven connection and potentially overload the smaller gauge wire. It's always best to use wires of the same gauge in each terminal position. This ensures a balanced load and a more reliable connection. It is always better to use the same specifications of wires within each terminal for the best performance and safety.
Finally, neglecting to label your wires is a recipe for disaster. When troubleshooting or making changes later on, you'll be faced with a confusing mess of wires and no way to tell which one goes where. Labeling your wires makes it much easier to identify them and avoid making costly mistakes. Use wire markers, labels, or even colored tape to identify each wire. Future you will thank you for it!
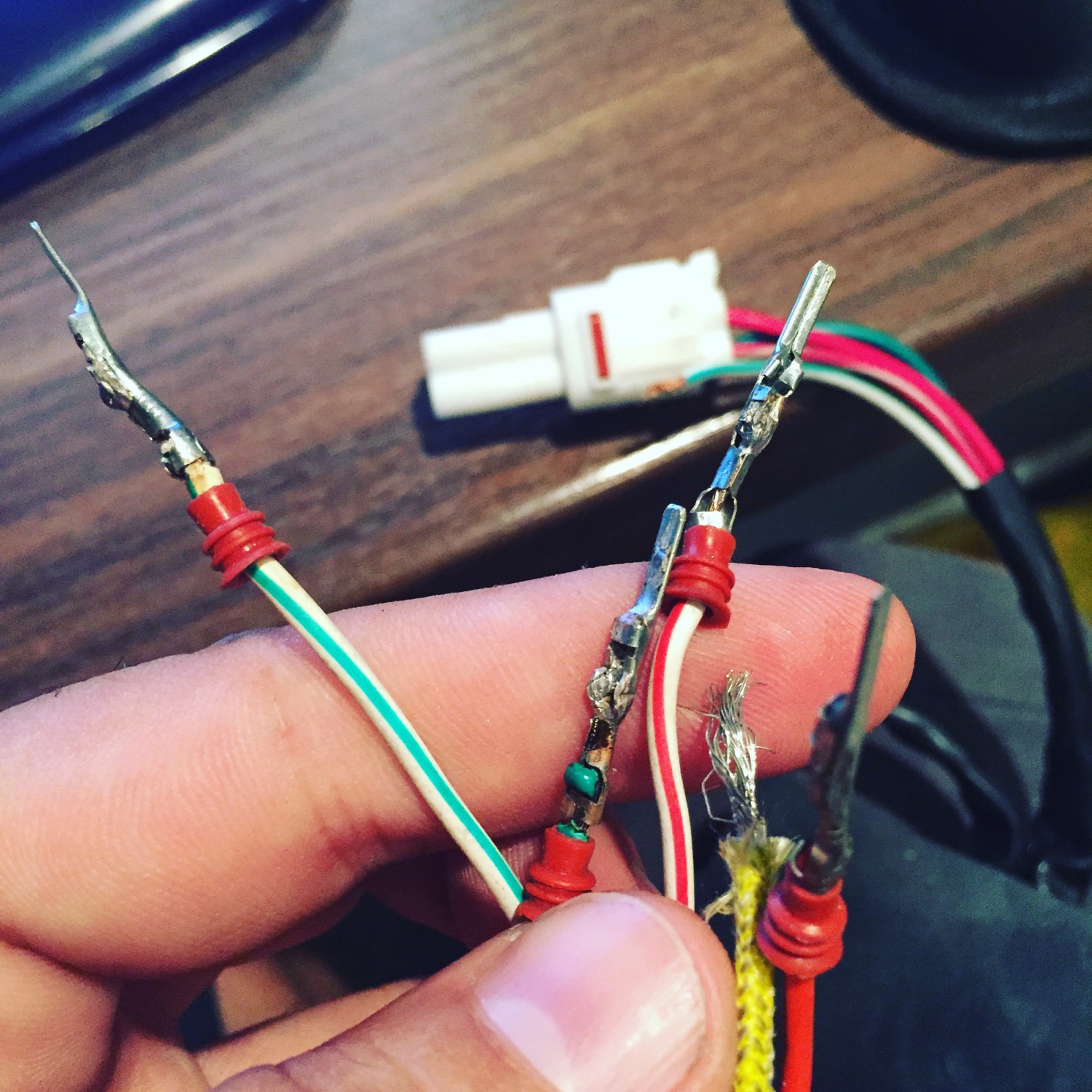
FAQ
5. Your Burning Questions Answered
Let's tackle some frequently asked questions about wire terminals to clear up any lingering doubts.
6. Question 1
Answer: While the total current might be within the limit, it's generally not recommended. Different gauges have different resistances, leading to uneven current distribution. The smaller gauge wire might overheat, even if the total current is safe for the terminal. Its best practice to use the same gauge wire for each connection point within a terminal.
7. Question 2
Answer: Overloading a terminal block can lead to a range of problems. The most immediate risk is a loose connection, which can cause arcing, overheating, and potentially an electrical fire. The terminal block itself may also be damaged, and the connected equipment might malfunction. Always adhere to the manufacturer's specifications for wire capacity to prevent these issues.
8. Question 3
Answer: Yes, there are! Some terminal blocks are specifically designed to accommodate multiple wires per terminal position. These often feature multiple connection points or larger clamping areas. They are great for distribution blocks. Always check the manufacturer's specifications to ensure that the terminal block is suitable for the number and gauge of wires you intend to connect. These multi-wire terminals can save space and simplify wiring, but correct usage is essential.
9. Question 4
Answer: While both stranded and solid wires are usable in terminals, they each have their own purposes. Solid core wires are more ideal for circuits that do not move. Stranded wires are more ideal for circuits that move often. It would be much safer to use stranded wires in circuits that vibrates often such as in a car, versus solid core wires that would break easily. Terminate the wires properly using correct connectors for the best and safest result!
