Impressive Info About What Is SLS Vs SLA
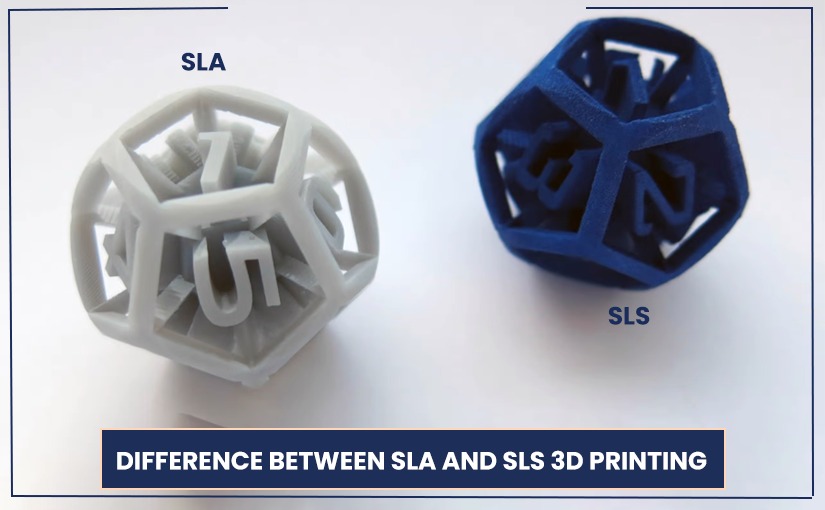
Difference Between SLA And SLS 3D Printing 3DIncredible
SLS vs. SLA
1. Understanding the Basics
Ever feel like you're drowning in acronyms when diving into the world of 3D printing? You're not alone! Two of the most common terms you'll encounter are SLS and SLA. While both are additive manufacturing technologies (fancy talk for 3D printing!), they work in fundamentally different ways. Think of it like this: they both bake cakes, but one uses a traditional oven, and the other uses a super-powered laser beam oven. Okay, maybe it's not exactly like that, but you get the idea!
The crucial difference boils down to the material used and the energy source employed to solidify that material into the desired 3D shape. Imagine trying to build a sandcastle with dry sand versus wet sand — same material, wildly different results. SLS uses powdered materials, while SLA relies on liquid resins. And instead of sunshine, they each harness different energy sources to make those materials stick together.
Why is this distinction important? Because the choice between SLS and SLA significantly impacts the final product. We're talking about things like material properties (strength, flexibility), surface finish (smooth or a little rough), cost, and the complexity of designs you can create. It's like choosing between a hammer and a screwdriver — both are tools, but you wouldn't use a hammer to screw in a tiny screw, right?
So, let's break down these two technologies, SLS and SLA, into digestible bites. We'll explore how they work, their strengths and weaknesses, and which applications they are best suited for. By the end of this, you'll be able to confidently decipher the 3D printing alphabet soup and make informed decisions for your next project. Get ready to level up your 3D printing knowledge!
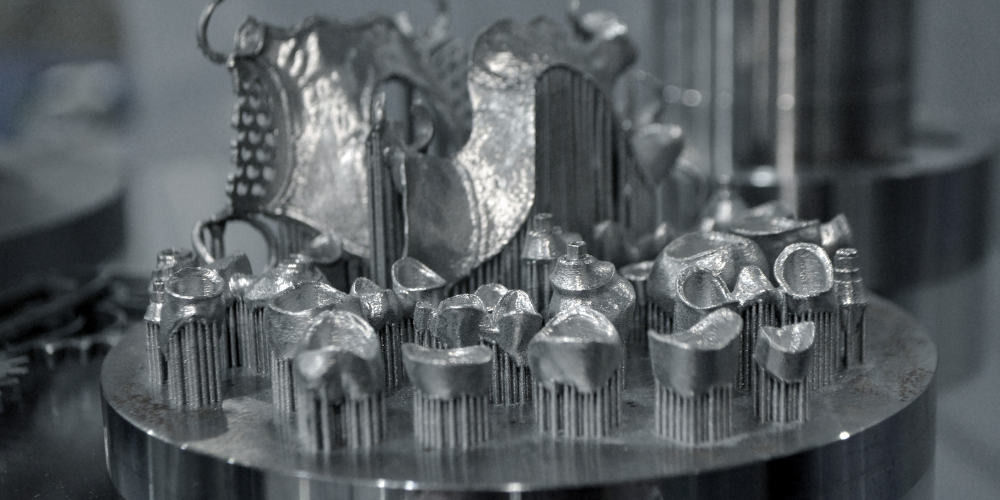
SLS Vs SLA Printing 3D Technology Comparison
SLA
2. How Stereolithography Works
SLA, which stands for Stereolithography, is one of the original 3D printing technologies. Picture a vat of liquid resin, kind of like honey but usually more colorful. Now, imagine a precise laser beam dancing across the surface of that resin. As the laser hits the liquid, it causes the resin to harden, solidifying a thin layer of your 3D model. This process is repeated layer by layer, with the platform holding the object slowly rising out of the vat, until the entire object is complete.
Think of it as "drawing" with light to create a 3D structure. The laser acts as your pen, the resin as your ink, and the computer-controlled system as your artistic guide. Each layer is incredibly thin, often just a few microns thick (that's thinner than a human hair!), allowing for incredibly detailed and smooth surfaces. This precision is one of the key advantages of SLA.
However, SLA printed parts often require support structures. Since the resin is liquid, some parts of your model might need extra scaffolding to prevent them from collapsing during the printing process. These supports are then carefully removed after printing, which can sometimes leave slight marks on the surface. It's like building a bridge — you need temporary supports until the main structure is strong enough to stand on its own.
SLA technology excels at creating parts with fine details, smooth surfaces, and high accuracy. It's a popular choice for prototyping intricate designs, creating jewelry molds, and producing dental models. If you're after precision and aesthetic appeal, SLA might just be your printing superhero. But remember, it's not all sunshine and lasers; the reliance on resin and support structures has its own set of considerations.
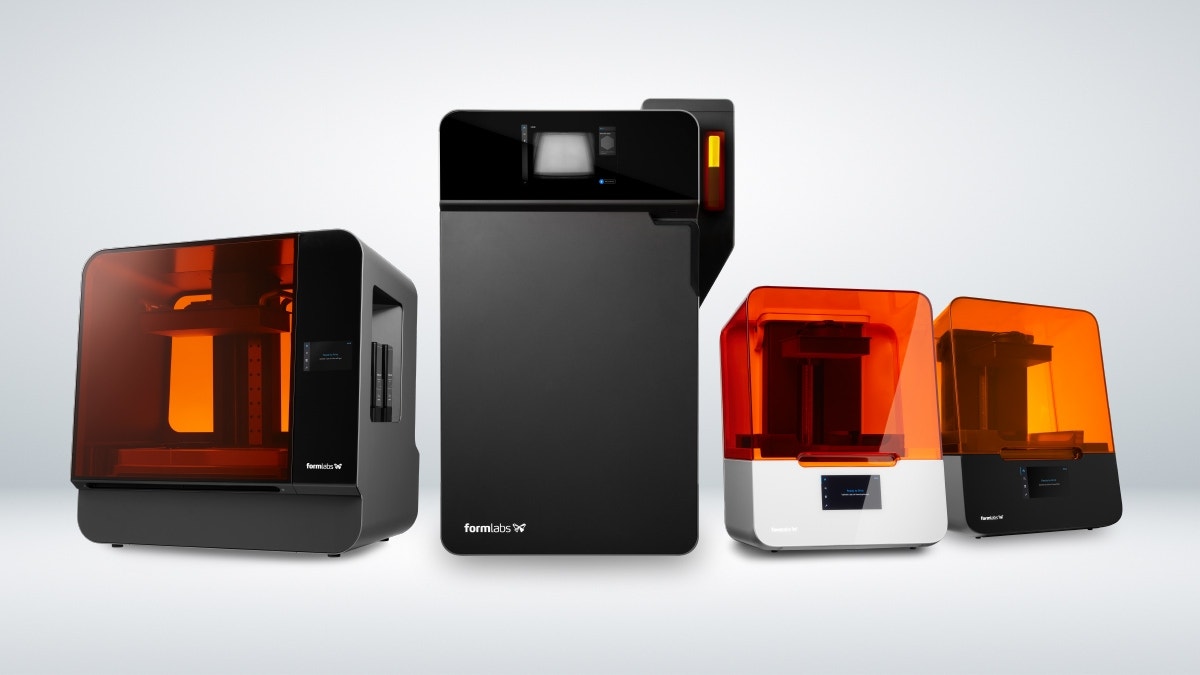
SLS
3. Unveiling Selective Laser Sintering
Now, let's shift gears to SLS, or Selective Laser Sintering. This technology takes a completely different approach compared to SLA. Instead of liquid resin, SLS uses a bed of powdered material, typically polymers like nylon, but sometimes metals or ceramics are also used. Think of it like a sandbox, but with highly specialized, finely controlled sand.
Instead of curing liquid, SLS uses a laser to sinter the powder particles together. Sintering is like welding, but without completely melting the material. The laser heats the powder just enough to fuse the particles together, creating a solid layer of your 3D model. After each layer is sintered, a new layer of powder is spread across the build platform, and the process repeats until your object is complete.
The beauty of SLS lies in its self-supporting nature. Since the object is surrounded by unsintered powder throughout the printing process, support structures are usually not needed. This means less post-processing and the ability to create more complex geometries. Imagine building a sculpture inside a container filled with styrofoam peanuts — the peanuts provide support, allowing you to create intricate shapes without worrying about them collapsing.
SLS is a workhorse when it comes to producing functional parts with good mechanical properties. It's often used in industries like aerospace, automotive, and medical for creating durable prototypes, end-use parts, and custom components. While SLS parts may not have the same level of surface smoothness as SLA parts, they are generally stronger and more resistant to heat and chemicals. It's like choosing between a fancy sports car and a rugged SUV — both have their strengths, depending on what you need to do.
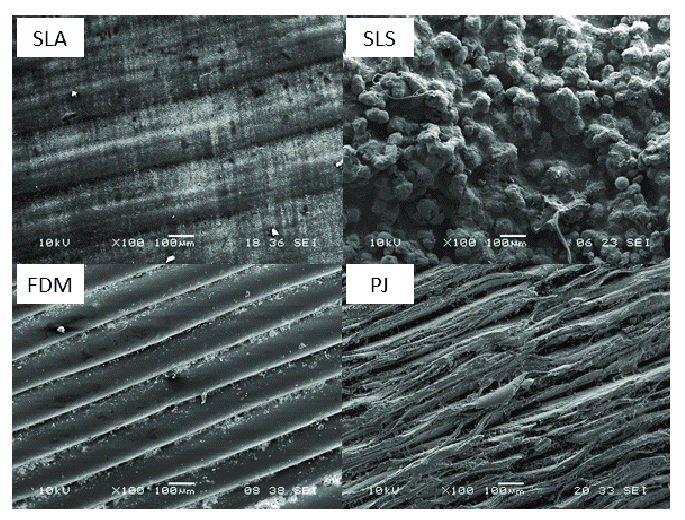
SLS vs SLA
4. Making the Right Choice
Okay, we've covered the basics of both SLS and SLA. But how do you choose the right technology for your specific needs? Let's recap the key differences:
Material: SLA uses liquid resins, while SLS uses powdered materials (typically polymers, but also metals and ceramics). This dictates the types of materials you can use for your projects. Resins tend to offer finer detail but might be more brittle. Powders can offer greater strength and heat resistance.
Surface Finish: SLA generally produces smoother surfaces than SLS. If aesthetics are a top priority, SLA is often the better choice. If you need a functional prototype that can handle some wear and tear, the surface finish from SLS is adequate, and the part may be more durable. You can usually improve the surface finish on SLS printed parts with some post processing like sanding, tumbling, or coating.
Support Structures: SLA often requires support structures, which need to be removed after printing. SLS is self-supporting, meaning it typically doesn't need support structures, reducing post-processing time and material waste. Support structures can cause ugly bumps on the surface of SLA parts, and removing them takes time and expertise.
Cost: Generally, SLA printers are cheaper to buy than SLS printers, but resin can be more expensive than some SLS powders. The overall cost depends on the size and complexity of your project, the materials you choose, and the volume of parts you need to produce. For small, precise parts SLA can be the right choice. For durable, strong parts in small or medium volumes, SLS is worth the investment.In short, SLA is your go-to for high-resolution parts with smooth surfaces, while SLS is the champion for functional parts with good mechanical properties. Think of SLA as the artist and SLS as the engineer.

Applications and Real-World Examples
5. Where SLS and SLA Shine
So, where are these technologies actually used in the real world? Let's take a look at some specific applications:
SLA Applications: Imagine a dentist creating a perfect model of your teeth for Invisalign aligners. That's likely an SLA printer at work. Jewelers use SLA to create intricate molds for casting rings and necklaces. Product designers use SLA to rapidly prototype new gadgets with smooth surfaces and fine details, such as enclosures and housings for consumer electronics.
SLS Applications: Consider the aerospace industry, where SLS is used to produce lightweight, durable parts for aircraft interiors, duct work, and custom tooling. The automotive industry uses SLS to create functional prototypes of engine components, brackets, and fixtures. Medical device companies use SLS to produce custom implants and surgical guides. SLS nylon parts are perfect for robotics, drones, and other mechanical applications.Both technologies are also used in educational settings, where students and researchers can experiment with different materials and designs to push the boundaries of 3D printing. Architects use SLA to produce scale models of buildings, and SLS to produce prototype furniture components.
Ultimately, the best choice between SLS and SLA depends on your specific needs and requirements. By understanding the strengths and weaknesses of each technology, you can make informed decisions and unlock the full potential of 3D printing. This understanding can also help you work with 3D printing services and make sure you ask the right questions to get the outcome you desire.
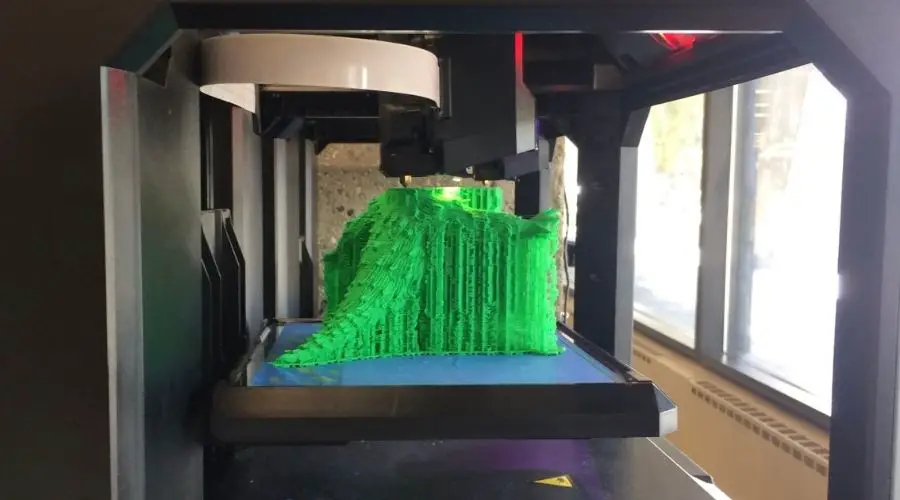
SLS Vs SLA A Comparison Guide Maker Industry
FAQ
6. Your Burning Questions Answered
Still have some questions? Here are a few frequently asked questions to help you solidify your understanding:
Q: Which is stronger, SLS or SLA?
A: Generally, SLS parts are stronger and more durable than SLA parts, especially when using polymers like nylon. However, the specific material used plays a significant role. Some advanced resins can achieve impressive strength, but SLS materials often have the edge in terms of impact resistance and heat resistance.
Q: Which is more accurate, SLS or SLA?
A: SLA tends to offer slightly higher accuracy and finer detail than SLS, especially for smaller parts. However, both technologies can achieve impressive accuracy with proper calibration and process control.
Q: Can I print metal parts with SLS or SLA?
A: SLS can print metal parts, but it requires specialized metal powders and a high-powered laser. This process is often referred to as Direct Metal Laser Sintering (DMLS) or Selective Laser Melting (SLM). SLA cannot directly print metal parts, but SLA can be used to create molds or patterns for metal casting.